7 Different Types of Forklifts: Mastering the Art of Material Handling
Forklifts, also known as lift trucks, allow workers to efficiently and safely move materials around warehouses, distribution centers, loading docks, construction sites, and more. Their sturdy prongs lift, stack, and transfer heavy payloads on pallets with incredible precision using compact yet powerful equipment.
With a growing range of electric, gas, diesel, and hybrid models now engineered for specialized lifting jobs, numerous forklift varieties exist beyond the basic sit-down forklift. Each offers unique capabilities for operators mastering the art of material handling.
Let’s explore 7 major forklift types and key differences driving the right equipment selection for filling operational roles safely and cost-effectively.
1) Electric forklifts: Versatile & Precise
Electric forklifts are powered by battery-supplied electric motors instead of internal combustion engines like gasoline or propane. They utilize rechargeable industrial batteries ranging from 24 to 96 volts which power electric motors to drive motors in the wheels. Electric forklifts are commonly used indoors due to zero emissions and quieter operation compared to combustion forklifts.
Electric forklifts come in a range of load capacities with the most common models able to lift between 3,000 to 15,000 lbs. They can utilize cushion or pneumatic tires based on surface use. Like other forklifts, they have two parallel forks on the front used to lift, stack and move heavy pallets or other objects in warehouses and tight spaces.
Some of the advantages of electric forklifts include:
1) Lower fuel and maintenance costs,
2) Reduced noise pollution in work areas,
3) Minimal heat and exhaust fumes ensuring more comfortable indoor operation,
4) Precision maneuverability in confined spaces thanks to automatic transmission,
5) Torque reaction that doesn’t jerk operators.
Electric forklifts deliver eco-friendlier, ergonomically smoother performance ideal for light- to medium-duty material handling uses.
2) Counterbalance Forklift: The All-Around Champion
The counterbalance forklift reigns as the most common sit-down lift truck design found in thousands of warehouses globally. These versatile workhorses account for over 80 percent of all forklifts in use today. Counterbalance models utilize rear-mounted weight plates opposite the forks to prevent forward tipping when heavy loads raise the prongs high. Side stabilizers provide further support. With lift capacities ranging from 3,000 to 40,000 pounds, counterbalance forklifts configured with fork extensions, rotating masts, or telescoping booms adapt to varied stacking needs. While larger counterweights sacrifice some maneuverability for brawn, newer lean-to-steer technologies bolster agility in tight spaces.
3) Reach Truck: Reaching New Heights in Warehousing
Whereas counterbalance forklifts spread capacity across hefty forks, reach trucks concentrate strength into slender telescoping prongs reaching horizontally and upward to 14 feet for lifting pallets onto high racks. Their compact chassis nimbly navigates down narrow warehouse aisles while extending forks deep within shelving cavities to precisely slide pallets into place – a maneuver impossible for bulkier forklifts. Customized for rack storage operations, reach trucks eclipse sit-down models for slotting bulky or oddly shaped loads requiring delicate finesse. Enhanced leverage from stabilizing legs allows heavy loads lifted high without compromising center of gravity. The operator platform often elevates as well for safely depositing pallets onto difficult top racks while avoiding repetitive strain from looking up awkwardly.
4) Order Picker: Picking Efficiency to New Levels
Order picking constitutes up to 65% of warehouse operating costs so optimized equipment reducing pick time proves tremendously valuable. Order picker forklifts allow individual selectors to fill large volumes of small orders simultaneously by organizing inventory on platforms at different heights to accommodate various-sized packages, containers, and components. The operator compartment either rides up narrow warehouse aisles atop elevating forks or travels vertically like an elevator alongside stationary shelving with built-in walkways for grabbing items easy to reach. Control panels featuring tallies of picked units boost rapid order fulfillment accuracy minimizing errors that delay shipments. Options like platform gates, safety harnesses, or railings prevent falls from heights adding reassurance whisking goods on and off upper tiers.
5) Rough Terrain Forklift: Conquering the Great Outdoors
The all-terrain capability allows rough terrain forklifts to traverse unfinished job sites littered with mud, cracks, and debris that easily immobilize standard forklifts. Massive knobby tires provide stability across uneven ground in wet, slippery conditions – apt for unpredictable outdoor climates. These heavy-duty lift trucks run on diesel fuel supplying plenty of torque for rugged motoring in low traction environments with steep inclines. Whereas counterbalance forklifts need smooth floors for secure footing while lifting loads above cement surfaces, rough terrain lift trucks maintain balance handling shifts in weight distribution even when stretched and reaching over obstacles. Robust construction protects components from weather exposure and abuse in high-impact zones. Specialized configurations with extending stabilizer legs, spotlights, safety cages, and customized forks stand up to abusive outdoor assignments.
6) Side Loader: The Specialist for Long and Bulky Cargo
Side loaders distinguish themselves from lift trucks facing pallets. Instead, these niche forklifts drive longways besides elongated loads like pipes, boards, steel beams, or awkwardly shaped cargo using overhead arms to pick stock straight from the side. Integrated railings enable side loaders to cradle extra-long materials firmly against durable side walls fronting industrial hauling trails. Hydraulic pivoting forks then rotate pieces up to 40 feet securely into position. Side access avoids troublesome maneuvering for positioning traditional forks under cumbersome loads that overhang the sides.
7) Pallet Jack: The Workhorse for Short Distance Maneuvering
In small stockrooms, retail spaces, and anywhere requiring light material transport over shorter distances, pallet jacks offer a smaller manual forklift alternative without the bulk or expenses associated with powered truck equipment. Still, rollers and hydraulic pumps make it easy for a single warehouse worker to move 2,500+ pound loads on flat smooth floors. Pallet jack forks slide easily under pallet bottoms for lifting. Pump handles then raise goods a few inches off the floor so loads can be manually wheeled from the dock to the stockroom or between aisle locations. Lowered forks set items down gently without sharp drops jostling products. In quick bursts across sites, their slim profiles cut through narrow openings better than hulking forklift structures ever could.
Conclusion
With capacities hoisting tons of materials up stories high and controls delicately finessed down to millimeter precision, mastery operating a spectrum of purpose-built truck models opens opportunities to streamlining productivity. Each solves unique rigging and handling challenges safely and efficiently. Simple control familiarity steers novices clear of preventable mistakes as experience blossoms towards fluid intuitions leveraging versatile equipment fuller potential.
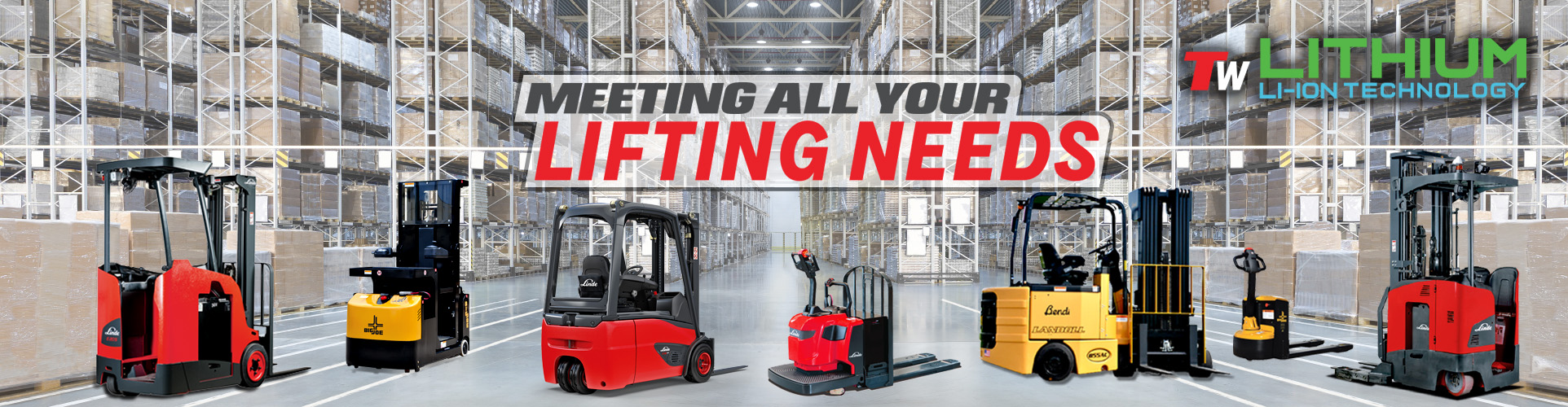
About Total Warehouse
Total Warehouse is a leading industry provider of top material handling products & cutting-edge intralogistics solutions for operational optimization. Our largest west coast fleet of equipment for rent, lease, and sale includes Linde Forklifts, UniCarriers, Big Joe Manufacturing, Landoll, Combilift, and Bendi. Give us a call at 833-868-2500 or contact us online.
Our product line features a wide array of electric of lithium battery powered forklifts, LPG propane forklifts, pallet jacks, and specialty lift trucks along with multiple attachments to support your applications. We also provide service, telematics for intelligent fleet management, engineering, pallet racking, operator and forklift training, and more.